750watt 3000rpm 220V Modbus/CANopen/EtherCAT Servo System with 23bit Absolute Encoder
Products Features:
Vector Tech. Focus on Servo system for more than 17 years.
More Flexible, More Accurate
Servo Drive + Servo Motor
Power Covers 200W-110KW
Single/Three Phase 220V/380V
Modbus / CanOpen / EtherCAT
Location, Speed and Torque Control Mode
2500 line incremental + Hall encoder; 2500 line incremental; 17/23 bit Tamagawa absolute encoder; 24 bit Nikon absolute encoder
Products Description:
Products | Servo Drive+Servo Motor |
Brand | Vector |
Model No. | VEC-VC1-00623M-M-E / 80ME-R7530A23-CF2 |
Power | 0.75KW |
Voltage | 220V |
Phase | Three Phase |
Rated Speed | 3000 rpm |
Rated Current | 5A |
Rated Torgue | 2.4 N.m |
Communication Protocols | Modbus/CANopen/EtherCAT |
Encoder | 2500 line incremental + Hall encoder; 2500 line incremental; 17/23 bit Tamagawa absolute encoder; 24 bit Nikon absolute encoder |
Product Details:
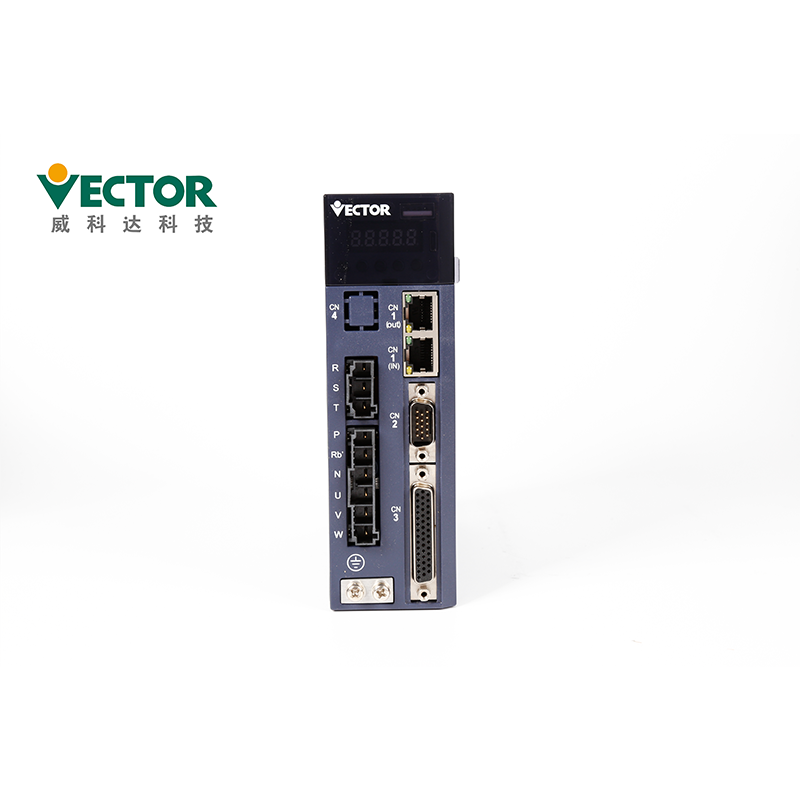
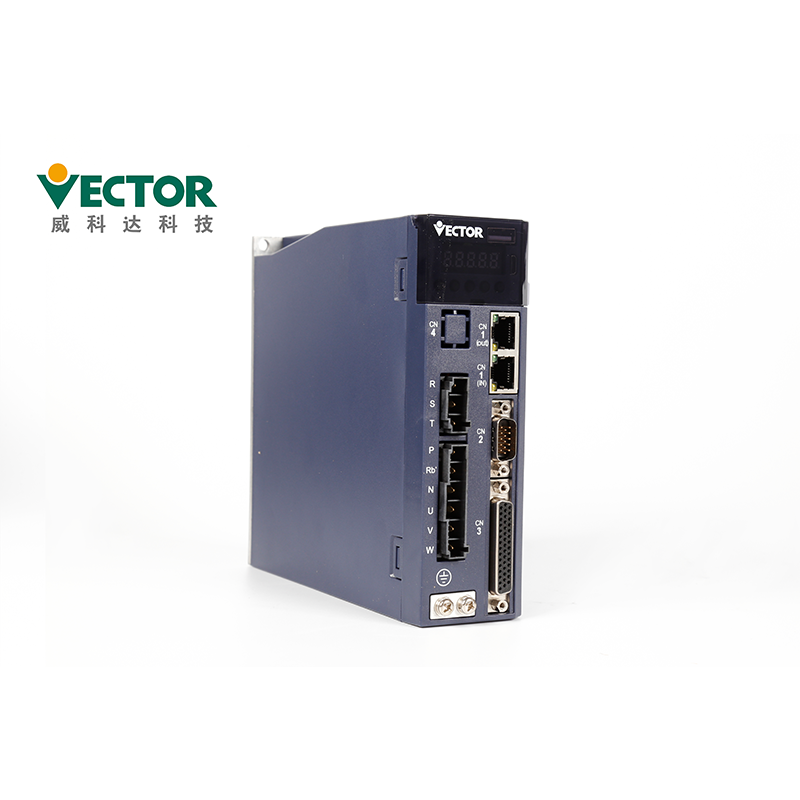
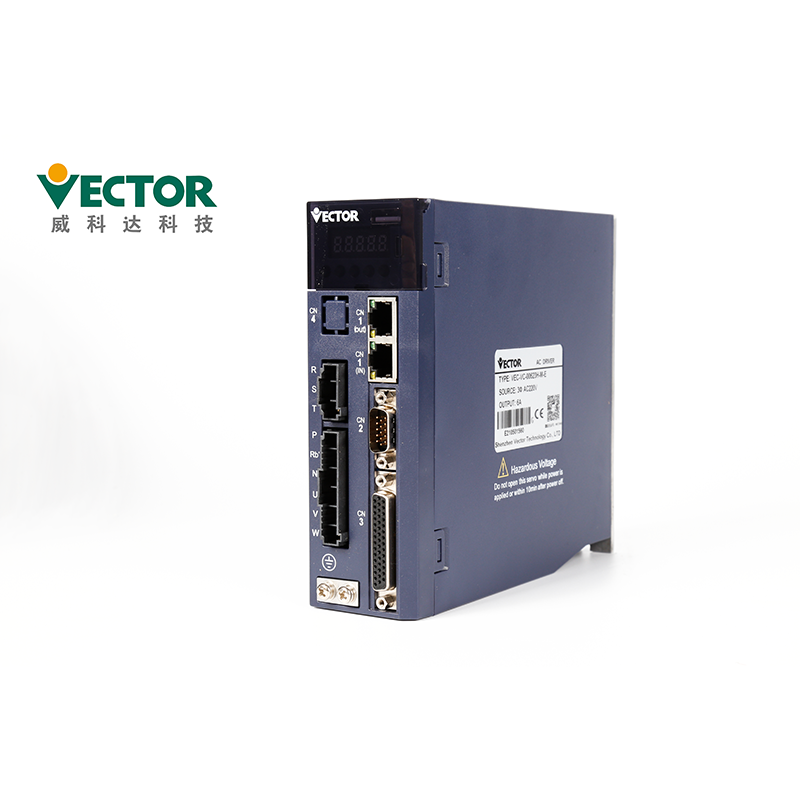
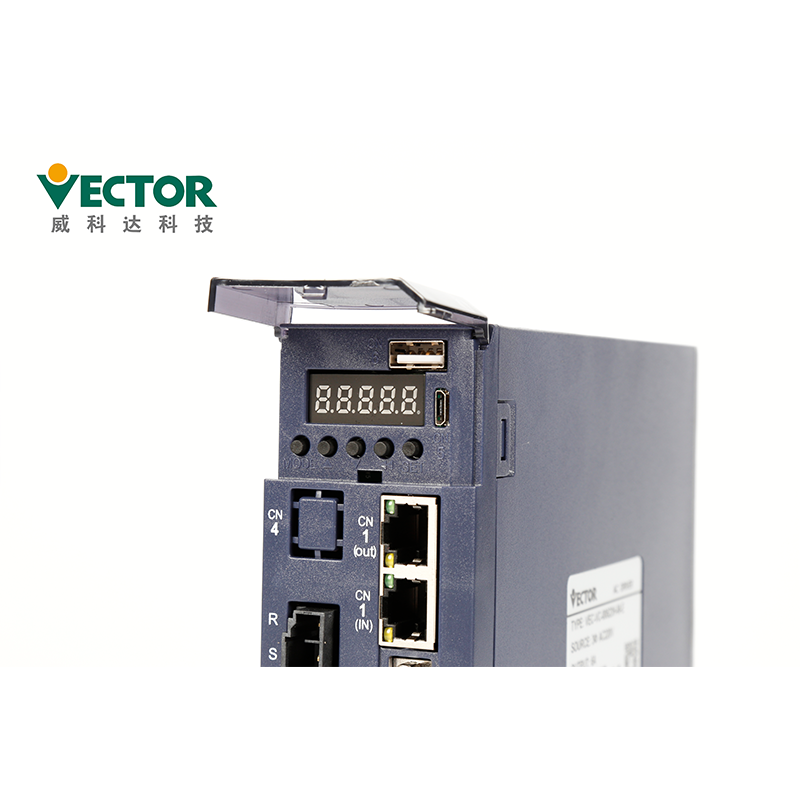
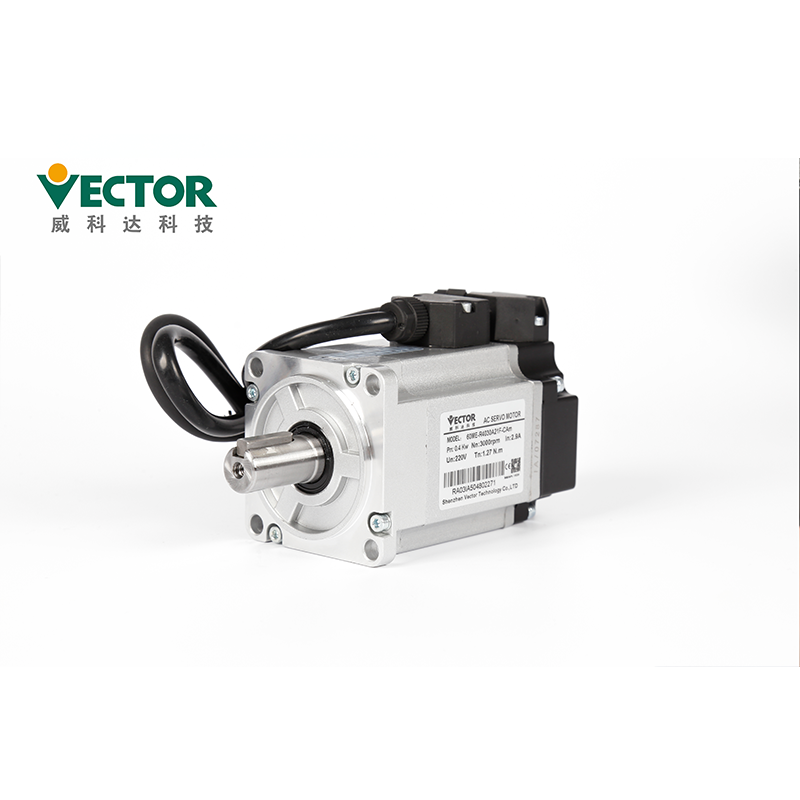
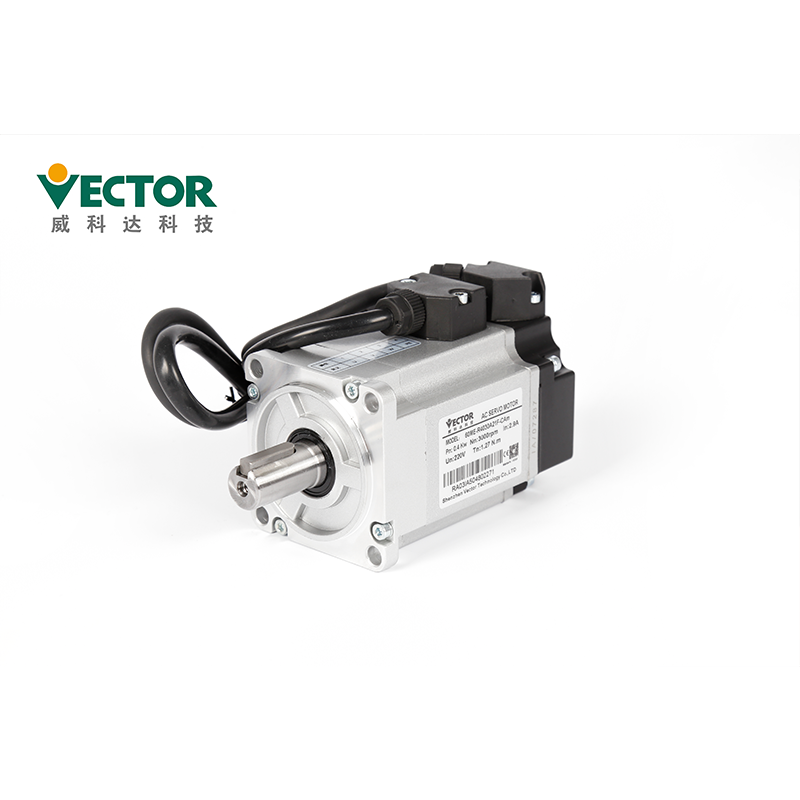
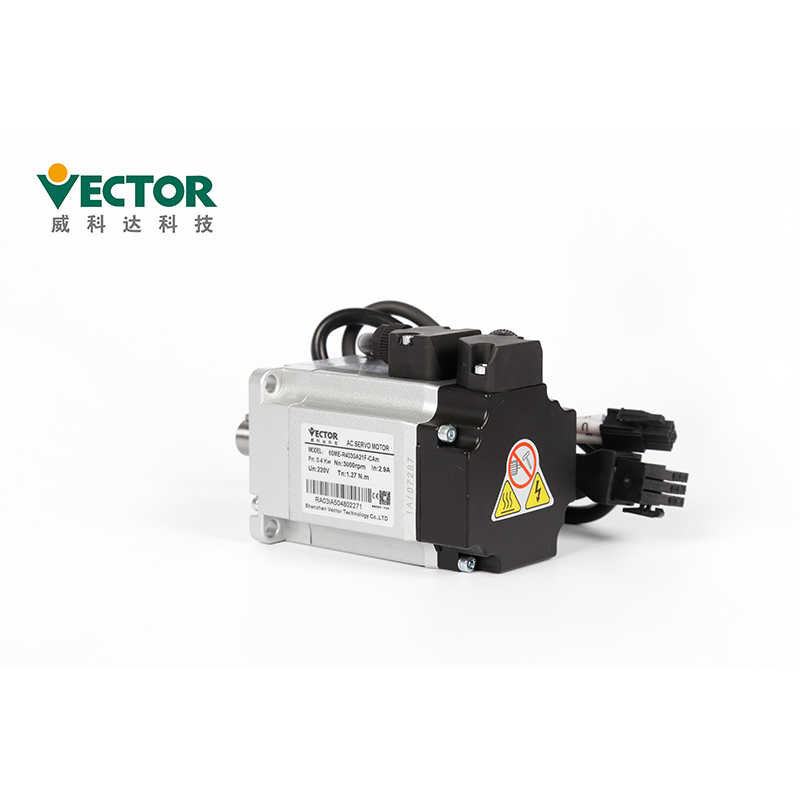
How to select the suitable Servo Drive model?
Servo Drive models:
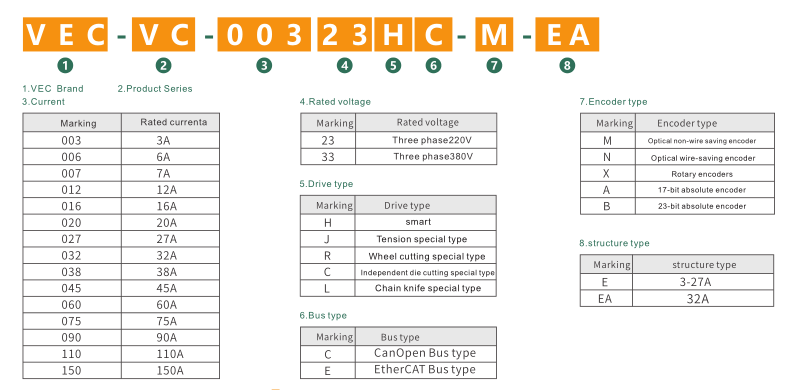
Servo Motors models:
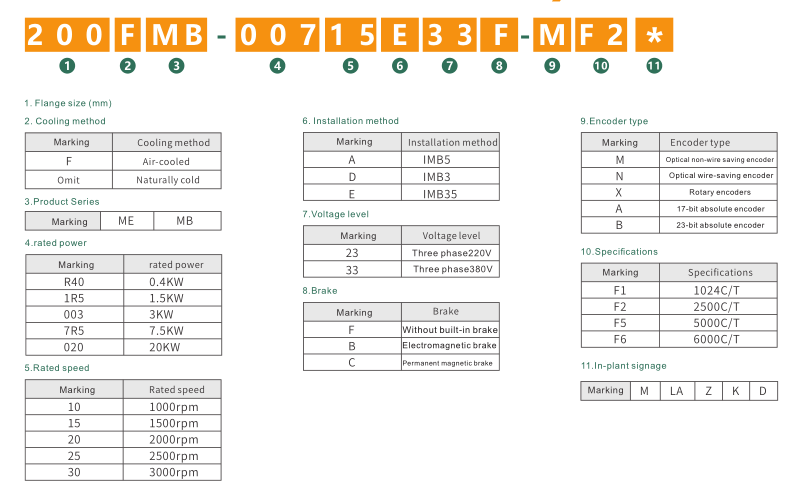
Encoder / Power Lines:
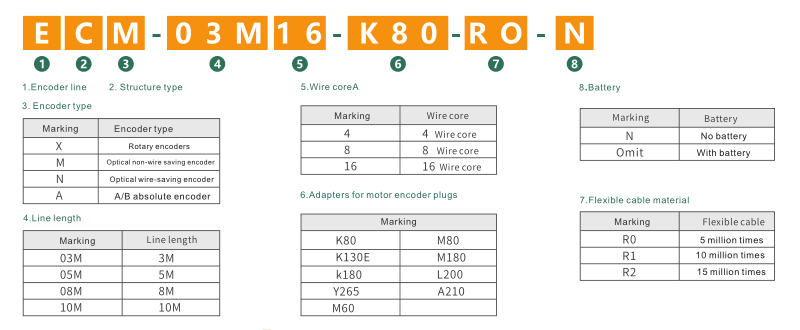
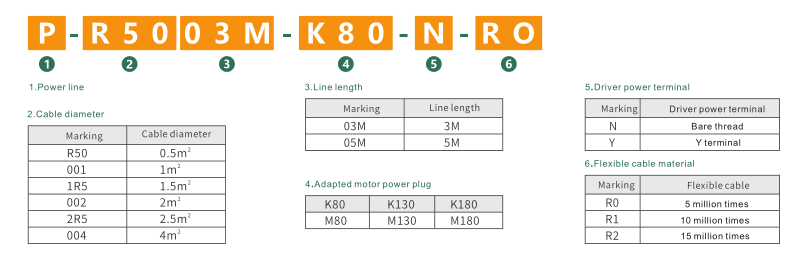
Packing details of Servo Drive | |||||
Products |
E1(3-6A) |
E2(7-12A) |
E3(16-27A) |
C015(32-38A) |
C022(45-60A) |
Ctn. Size |
280*208*78 |
280*208*112 |
375*290*155 |
440*296*288 |
510*305*325 |
Packing details of Motion Controller | |||||
Products |
VA Motion |
VA Expansion |
VE Motion |
VE Expansion(32) |
VE Expansion(32) |
Ctn. Size |
176*165*78 |
127*75*70 |
144*128*69 |
176*164*78 |
316*164*78 |
Payment Terms | |||||
Samples: 100% before delivery by Western Union. | |||||
Bulk Orders: 30% deposit, 70% before shipping by T/T or Western Union. | |||||
Production Time | |||||
Small orders 3-5 work days | |||||
Production capacity can reach 1000 kits per month. |
Our Services:
1.17 years more experiences focus on Motion control filed, Obtained a number of patent certificates on Servo Drives and Motion controllers; 2.24 months warranty for all of our main products(Servo drive+servo motor, Motion controllers); 3.Face to Face Technical Support on programming or installation; 4.Door to door services if necessary. |
FAQ
Q1. How to select the suitable model? Q2. How to set the programming system? Q3. What's the power range about our servo system? Q4. What's the encoder feedback interfaces we using? |
Accessories:
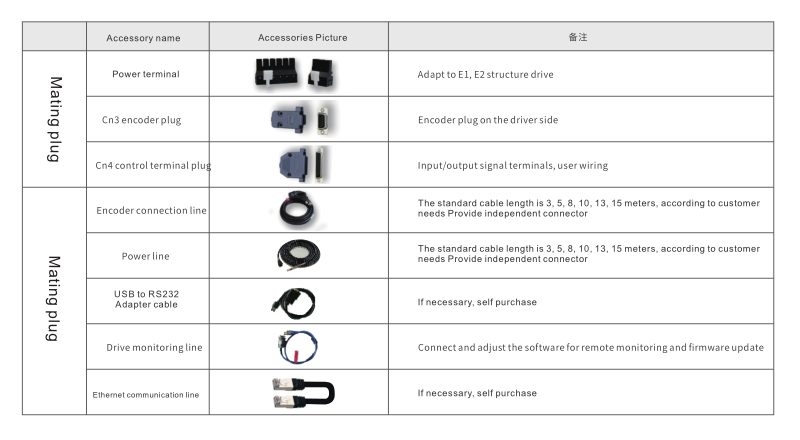